Study of Film Cooling with Shaped Holes for a Hydrogen Combustion Turbine Blade
Shigemichi Yamawaki, Takashi Maya and Shohachi Yasu
Aero-Engine & Space Operations
Ishikawajima-Harima Heavy Industries
Mizuho-machi Nishitama-gun Tokyo 190-12 Japan
Abstract
A hydrogen-combustion turbine system is needed for clean power generation with high efficiency in a future power system. In the WE-NET project, we researched the cooling configuration of a turbine blade for this turbine system. To protect the turbine blade from anticipated high steam gas temperatures, we chose to adopt shaped diffuser holes of high film-cooling performance. In order to design such a cooled blade for the pilot plant, basic film cooling tests were carried out for estimating the cooling performance of new shaped holes. In our results, we found about 20% to 30% higher film cooling effectiveness for the best shaped hole when compared to the current shaped-hole style. With the new shaped holes, we estimate about a 15% increase of film effectiveness for the whole blade, which means about 20% decrease of coolant flow rate compared with current high-performance cooled blades in an aero-engine.
1. Introduction
The WE-NET project [1] aims to establish technologies for constructing a hydrogen energy network on a world-wide scale based on non-carbonaceous renewable energy. In this project, we are considering a hydrogen-combustion turbine system for clean power generation with high efficiency in a future power system. To realize high efficiency of this clean power generation, the operating gas temperature should be as high as possible. Based on our aero-engine turbine-cooling technologies, we are trying to develop a 1700degree Class hydrogen combustion gas turbine. We research the cooling configuration of a turbine blade for this turbine system.
A typical cycle of a hydrogen combustion turbine system for this research is based on the cycle studied at the Graz University of Technology [2]. Figure 1 shows a diagram of this cycle which is constructed with a top and the bottom cycle. The top cycle is a simple gas cycle. The bottom cycle resembles a steam turbine cycle. Although the bottom cycle contributes to high efficiency, the turbine inlet temperature of the top cycle is a key factor for highly efficient power generation. A high temperature turbine for the top cycle is most difficult to develop because it has many stages and all turbine blades may be cooled.
To protect from the higher heat flux on a turbine blade compared to current gas turbines, we believe high performance film cooling is needed for a hydrogen-combustion gas-turbine blade. Since shaped-hole film cooling has been a promising way to increase film cooling performance in a recently developed aero-engines, we sought further enhancement of cooling performance with new shaped holes. We considered a Thermal Barrier Coating for protecting the blade surface, too. We chose 4 kinds of new shaped holes which can drilled by laser on a ceramic coated blade surface. To compare film cooling performance, we carried out basic tests on a convex curvature surface which simulates a blade suction surface.
2. Experimental
In a case where both the free-stream and coolant are dry steam, it is expected that there is no big difference in the phenomena of a film cooling process when compared to an air cooled blade in a conventional gas turbine. For convenience, we chose air instead of steam for a basic test.
Figure 2 shows the test apparatus. Air is supplied from a compressor to the test section with pre-heating by a combustor. Film cooling holes are located on a convex surface which has an equivalent ratio of blade suction surface curvature to cooling hole diameter. The hot free stream gas temperature was set at 500degree. The cooling gas temperature was about 20degree. This gives a temperature ratio selected yield an equivalent density ratio, DR=2, of the actual operation conditions.
The wall downstream of the cooling-hole row is almost adiabatic because ceramic blocks and glass wool is need. To measure the adiabatic wall temperature, thermocouples are embedded in the ceramic surface. In order to measure pitch-wise average temperature, a small copper piece is attached to a junction on each thermocouple. Three thermocouples are embedded for 1 hole pitch. Film effectiveness is defined as,
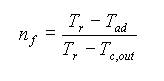
where Tr is recovery temperature, Tad is adiabatic wall temperature, Tc,out is coolant temperature at hole exit.
Figure 3 shows styles of the tested cooling holes. Four styles of new shaped holes, TP3 to TP6, are constructed as a basic cone shape for easy manufacturing by laser drilling. Hole TP3 is a simple cone shape. TP4 and TP5 are enlarged only pitch-wise. TP6 has a triangular section shape. A circular hole TP1 and the current shaped holes TP2 are also tested for comparison. The inlet cooling hole diameter is equal as 4 mm for all cooling holes. TP2, TP3, TP4 and TP6 have almost the same area ratio between hole inlet and exit; TP5 has larger area ratio.
Experiments are conducted for 5 kinds of blowing ratios, BR=0.5 to 2.5. The blowing ratio is defined as the ratio of cooling hole inlet mass flux to free-stream mass flux.
3. Results and Discussion
Figure 4 (a) compares film cooling performance for 6 kinds of cooling holes at a location not far downstream of the holes, X/D=10, where X is a distance from hole exit and D is a diameter of hole exit. Figure 4(b) shows the ratio of averaged film effectiveness in the near downstream of the cooling holes. The results of TP2 are the basis for the ratio, so TP2 data becomes identically 1.0. At lower blowing ratios, there is no big difference because coolant flow velocity is sufficiently low to maintain film flow attached to the wall. But at higher blowing ratios, there are big differences depending on the style of hole. TP4 and TP5, which show higher effectiveness, have the same hole height but different hole exit width. We understand that the hole exit width is the most important characteristic for high performance shaped film holes. TP5 has an effectiveness 20 to 30% higher than the current shaped hole.
In order to estimate the advantage of cooling performance by use of the new shaped hole, we conducted a 1-dimensional heat-transfer analysis for stator and rotor blades of the first stage of a hydrogen-combustion turbine. The turbine inlet temperature is 1700degree and pressure is 50 ata. Heat transfer characteristics were estimated in this analysis based on our aero-engine experience. We assumed a 15% increase of film effectiveness for whole blade in this analysis. Figure 5 shows results that coolant flow reduction is 17% to 18% compared to a current high performance aero-engine.
4. Conclusions
In this experiment, we compared the film effectiveness for current and new shaped holes. TP5, which has the largest diffusing area ratio and the largest hole exit width, showed the highest effectiveness. Advantages over the current shaped film hole is about 20% to 30%. This is equivalent to about 20% reduction of the cooling gas flow rate. We expect to develop a high-efficiency hydrogen-combustion turbine with the new shaped film cooling holes.
To confirm the increase of cooling performance, we are conducting a cooling performance hot-air wind tunnel test for a 2D scaled-up model blade with the new shaped hole TP5. We are also planning a high-temperature turbine-cascade test with a hydrogen-combustion combustor in the near future.
Acknowledgment
This work has been conducted under a contract from the NEDO (New Energy and Industrial Technology Development Organization) and the JAPEIC (Japan Power Engineering and Inspection Corporation) as a part of the New Sunshine Program of MITI (Ministry of Industrial Trade and Industry). We appreciate their advice and support.
References
(1) M. Murase, "R&D Plans for WE-NET", Proceedings of IHCE'96
(2)H.Jericha et al, "Towards a Solar-Hydrogen System", 1991 ASME COGEN-TURBO IGTI-Vol.6
|